Soybean hulls facilitate next-gen battery function
Leveraged checkoff dollars draw NASA funds to KU, build industry collaboration
Lithium-ion batteries: you can find them in cell phones, computers, vehicles and even aerospace technology. You might say they power our world, but they also have shortcomings. They carry substantial risk of failure due to internal instability – cue the Federal Aviation Administration’s ban on using Samsung Galaxy Note7 phones aboard planes, tech companies admitting that exploding laptop batteries are unpreventable, and even a Tesla vehicle’s spontaneous combustion on a freeway.
Dr. Lin Liu in Kansas University’s department of mechanical engineering is looking toward next-generation lithium-sulfur batteries to solve the degradation issues with current lithium-ion batteries and expand upon the life and capability of such batteries.
Battery production and utility make up a multibillion-dollar industry. The lithium-ion batteries currently in the marketplace consist of a sandwich structure with the negatively-charged anode side and positively-charged cathode side with a liquid electrolyte solution in the middle that enables the internal reaction by conducting the ionic current. Liu’s model of lithium-sulfur batteries uses a similar sandwich structure containing pure lithium metal on the anode side, a solid ceramic-based polymer separator and a carbon matrix lined with sulfur particles on the cathode side. The carbon matrix is composed of carbonized soybean hulls.
Sulfur is an ideal material in next-generation batteries because it is economical and has an abundance of energy. When it reacts with lithium metal, “it could be a gamechanger,” Liu says. It does, however, need carbon in the mix in order to conduct electrons and complete the reaction. A carbon source provides the pathway.
“We are building a rechargeable battery so electrons come and go,” Liu explains. “The reason we put soybeans in the cathode side of the battery is to move those electrons back and forth.”
Liu says the soybean can be used two ways to produce a battery. The first way mimics traditional electrode formation by burning the soybean hull to carbonize it, mashing it up, then mixing it with sulfur particles. The second way, which is a key concept in Liu’s research project, is to create a sponge-like matrix consisting of porous carbon from soybean hulls and spraying sulfur particles into the matrix to form the sulfur electrode.
In the second method, “the soybean provides a supporting matrix as well as a conductive pathway,” Liu says.
Why soybeans? It’s simple – soybeans check all the boxes for how the carbon source needs to act.
“What we really want to achieve is to use a soybean to build this carbon matrix,” Liu says. “We have to find something with a very high carbon content that also has manageable purity and ample porosity. If you put all those things into an evaluation rubric, soybeans came out on top.”
Liu has been researching batteries for 15 years and previously sourced a carbon polymer from a commercial vendor. He realized that an alternative, applicable carbon source was growing in fields around him.
“I thought we should definitely use Kansas-grown soybeans to produce what we really want,“ he says.
Currently, Liu is sourcing the soybeans used in the research from local farmers markets. Those vendors offer green soybeans in the pod, which adds time to the carbonization process since hulls are the key soybean component in the battery formulation. One of Liu’s goals is to find a source for quantities of processed hulls.
According to representatives of the processing industry, about 95 percent of the demand for processed soybean hulls is using them as an additive in animal feed. Additional uses are growing, including on mushroom farms. Batteries could contribute to the added-value of soybeans with large scale adoption of hulls in manufacturing.
This summer, Liu and his team wrapped up year one of the research project, which was to prove the concept that soybeans can be used to produce a working, rechargeable battery paired with a lithium metal. The Kansas Soybean Commission approved funding for year two of the project, which builds upon the design and fabrication of solid-state lithium-sulfur batteries.
Liu leveraged the checkoff dollars granted by the Commission to apply for and receive project funding through NASA. Initially, KU secured nearly 200,000 dollars in funding from the year one findings to go toward enhancing the sustainability and resilience of the batteries for space application. Recently, Liu and his team confirmed that they would receive over one million dollars from NASA to continue building upon the function and safety of their batteries. Liu collaborated with research and industry partners from Kansas State University, Wichita State University, Spirit Aerospace, Argonne National Laboratory and others to secure the additional funds.
“We are proposing a safer, more powerful and more reliable battery for space applications,” Liu explains.
Using batteries for aerospace technology requires a highly-safe, stable battery. That is a key reason Liu decided to pursue production of a next-generation battery from the start.
“You hear in news about battery explosions and it’s hard to avoid that with traditional batteries,” Liu notes. “Lithium-sulfur is much safer – you can cut it, you can puncture it, you can bend it and won’t cause detriment.”
Safety and reliability are just a few of the potential benefits for these next-generation batteries. There is an environmental incentive; lithium-sulfur batteries tout higher energy output, increased use capacity per recharge, and simple recycling.
Liu says, “The energy you could get from a lithium-sulfur cell is four to five times higher than traditional lithium-ion batteries, so, by nature, you are using fewer batteries.”
Traditional lithium-ion batteries degrade and can be more challenging to recycle, Liu adds, but the individual components of lithium-sulfur batteries are easier to recycle. Enhancing the recycling opportunities are planned for further into the research process.
The ultimate goal is to bring these lithium-sulfur batteries to the market, which could be 10 years from now, Liu says, though it is not too early to start enticing investors and industry interest in the project. In March 2023, Liu and his team attended the International Battery Seminar in Orlando, Florida, to do just that.
Soybean use in battery applications as a concept is not new. Projects in locations as close as Pittsburg State University and over at University of Louisville in Kentucky are examining soybean hulls in their ability to boost lithium-ion absorption or determining their function in supercapacitors. Liu’s project concept takes a different approach in the battery manufacturing to develop the solid-state interior. The novel electric-field-augmented ultrasonic spray pyrolysis, or EFAUSP, in Liu’s research creates the sulfur-carbon matrix.
Dr. Liu joined KU’s department of mechanical engineering in 2013. A native of China, he studied for his undergraduate and graduate degrees there before moving to the states in 2008. He received his Ph.D. in mechanical engineering from Iowa State University of Science and Technology and completed post-doctoral work at Michigan State University before landing at KU.
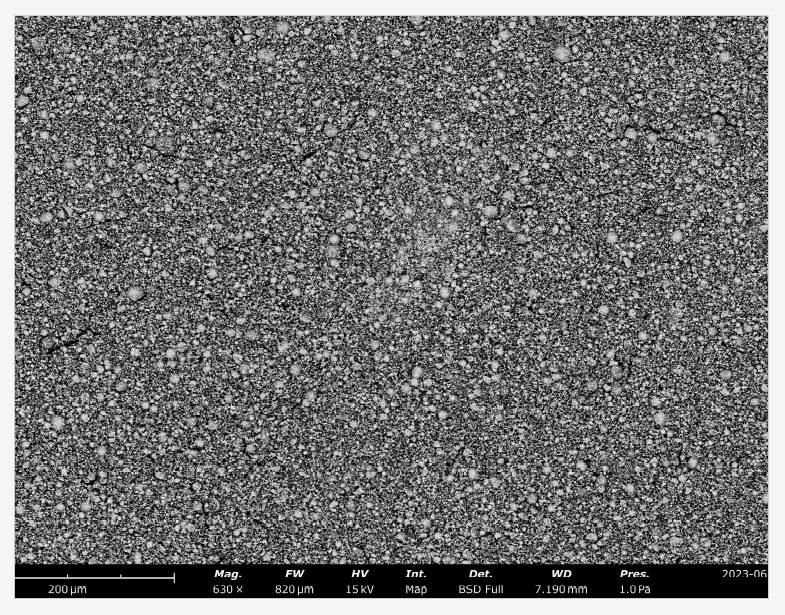
A magnified image of the porous carbon matrix made from soybean hulls. Sulfur is sprayed into this matrix, which comprises the cathode side of the battery opposite pure lithium metal.